Heavy industrial applications such as manufacturing, chemical processing and oil-and-gas refining use cooling towers and other equipment to cool the water integral to their operations. As environmental regulations and challenging market conditions place higher demands on these industries, improved cooling technologies are emerging to help address the challenges.
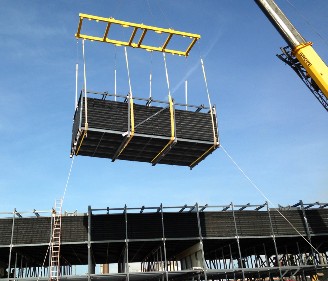
In the oil-and-gas industry, many cooling towers currently in service were built as part of the original refinery construction, and they are fast approaching the end of their service lives. In order to meet modern production demands and industry requirements, these towers must be upgraded or replaced with more efficient products, and better long-term maintenance plans must be instituted.
Cooling Tower Operation and Types
Cooling towers are specialized heat exchangers that reduce the temperature of water by bringing it in contact with air. Water, which has been heated by an industrial process, is pumped to the cooling tower through pipes. The water sprays through nozzles onto banks of heat transfer material called fill, which slows the flow of water through the cooling tower and exposes as much water surface area as possible for maximum air-water contact. As the water flows through the cooling tower, it also is exposed to air that is pulled through the tower by an electric-motor-driven fan.
When the water and air meet, a small amount of water is evaporated, creating a cooling action. The cooled water then is pumped back to the process equipment, where it absorbs heat. It then will be pumped back to the cooling tower to be cooled once again.
Different types of cooling towers are suited for different industrial cooling needs. Field-erected towers (FEP) are constructed on site, designed for large heat loads and are engineered to address the specific application.
Field-erected towers are well suited for power and heavy industrial uses, and they are frequently found in refineries and chemical processing plants.
Werksmontierte Türme (FAP) are constructed in modules at a manufacturing facility and then shipped to the processing plant in as few pieces as possible for final assembly. Factory-assembled towers are available in many cooling capacities and box sizes, and they include standardized mechanical and structural components.
For refineries and chemical processing plants, open-circuit wet cooling towers — coupled with shell-and-tube or plate-and-frame heat exchangers — provide an economical method for rejecting heat. These towers are designed to wet bulb temperature and can cool water to a lower temperature than some other technologies. But, refineries and processing plants also employ other methods to achieve cooling.
Luftgekühlte Wärmetauscher
Evaporative cooling towers such as those described above use heat transfer fill to effectively distribute the hot process water and increase its surface area for more efficient cooling. The trade-off is that many fill types require relatively clean water to run effectively. Lower quality water containing particles and debris will clog the fill and reduce performance.
For situations where water is scarce, unavailable or expensive, air-cooled heat exchangers are an alternative cooling technology. Air-cooled heat exchangers are built to handle the high heat loads common in oil-and-gas and chemical processes, require infrequent maintenance and do not evaporate water for cooling.
Air-cooled heat exchangers use only airflow to cool hydrocarbon products and other fluids in tubes. Hot process fluid from the plant flows through fintubes while cooling air flows across them. Air-cooled heat exchangers work well for higher temperature hydrocarbon applications. These heat exchangers are employed by the oil-and-gas industry because water or water chemistry maintenance is not required, and they do not create the vapor plume of evaporative towers. However, because they are designed to dry bulb temperature, they cannot cool water or process fluids to temperatures as low as wet cooling towers.
Other specialized heat exchangers such as evaporative condensers and closed-circuit fluid coolers are also employed to cool processes and fluids throughout chemical plants.
Challenges for Oil and Gas
In oil-and-gas refineries, industrial equipment is often jacketed or sleeved with flowing water to cool fluids and absorb process heat. This equipment generates a large heat load that can disrupt operations if not properly handled. Cooling towers are used to cool this process water for reuse. The towers must be able to handle the heat load as well as any problems unique to the industry. Leaks in the process can cause hydrocarbons to contaminate the cooling water and vice versa. Lower quality, nonpotable water often is used to cool plant processes. Meeting environmental regulations limiting hydrocarbons, water usage and drift rates present challenges to plant operators. New industry regulations often require cooling towers to lower the drift rate to 0.0005 percent of circulating water flow, which can be difficult to achieve in older evaporative cooling towers. Many cooling towers currently in use are not equipped to handle these demands.
A few decades ago, field-erected towers commonly used wood structural members. These cooling towers are coming to the end of their service lives, experiencing mechanical failures, requiring unplanned maintenance that interferes with production and impacting facility productivity. The heat transfer fill in the towers also degrades over time, getting plugged with waste from dirty cooling water and breaking down from the weight of debris.
A good portion of the industry is in need of new towers and better long-term maintenance plans. “A lot of the existing cooling towers are either aging out or suffering from lack of proper maintenance,” says Alan Christian, president of Christian Power Equipment Inc., a company that specializes in equipment for power, process and pollution control. “It’s significant enough that I would call it a trend [in the industry].”
Replacing Old Towers
Replacing aging wooden cooling towers is a challenging undertaking. Because they are integral to the production process, maintenance, repair and replacement must be accomplished within short scheduled outage periods. Some replacements are done one cooling cell at a time, allowing the plant to continue to operate — a practice known as online construction. Rental of temporary cooling equipment often is necessary.
In order to combat replacement logistical challenges and high costs, cooling tower manufacturers offer both field-erected and factory assembled towers. Refineries and chemical plants can replace old, deteriorating towers with modular field-erected towers or pre-assembled package towers that are project and site specific.
“A lot of these refineries were established between 1950 and 1970 when the original towers went in. They built up the refineries around [the towers],” says Pam McLaughlin, sales engineer at Hastik-Baymont Inc., a company that specializes in engineered equipment solutions for the oil-and-gas and process industries. “Most places, unless they’re new grassroots refineries, don’t have a whole lot of lay-down area to do tower repairs or replacements on a basin that’s already erected. There’s just not a lot of available space.”
Field-Erected Solutions: To work with these constraints, some manufacturers have modularized the production and field-assembly processes for counterflow, field-erected towers. Often, modular cooling towers erect faster and require less site lay-down area compared to traditional tower construction methods while offering the same capabilities to keep up with large heat loads. Modular components can be shipped “just in time” to the job site, reducing construction duration and manpower requirements. Assembly processes are safe, and uniform factory-assembled modules ensure consistent product quality.
Factory-Assembled Tower Considerations: Factory- assembled cooling towers are a viable alternative for oil-and-gas applications. They offer fast delivery and installation and more site placement flexibility. They also allow for shorter outages and loss of production time. In case of expansion, additional cells may be added to provide more cooling capacity. Factory-assembled cooling towers designed for process applications are available in either counterflow or crossflow designs and include heavy-gauge, corrosion-resistant structural components and mechanical drive trains built for reliability and long service life.
In conclusion, as environmental and market demands put pressure on oil-and-gas refineries and chemical processing plants, they must take measures to ensure their facilities and equipment are modern and efficient. Old deteriorating cooling systems must be replaced by new technologies, made with durable materials and components, backed by reputable manufacturers, and supported by knowledgeable engineers and service technicians. Cooling systems also must be part of comprehensive monitoring and maintenance programs that extend the equipment’s profitable service life and alert plants to potential problems before a crisis arises.