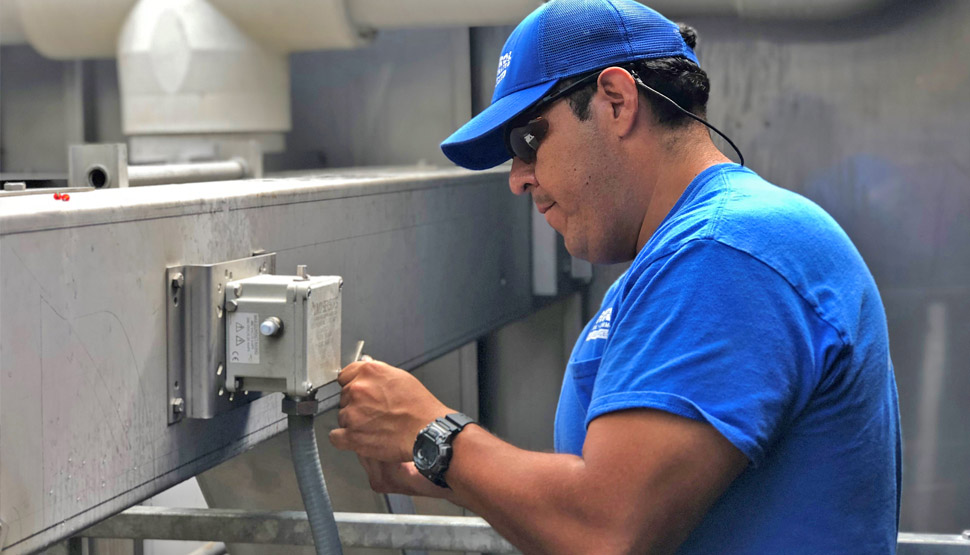
Many service contractors and cooling tower owners take a “squeaky wheel” approach when it comes to maintenance and repair. They replace a component only after it breaks, or they perform a repair when a component failure is imminent.
How can service providers provide more value? Take a proactive approach to maintaining cooling towers.
Diagnosing maintenance issues often begins with inspection of mechanical equipment and components subject to wear and tear – for example, motors, gearboxes or belt drives. Tower cleanliness is also a major consideration, especially with increasing regulations and ASHRAE standards. This includes water chemistry, fill media and more.
Another overlooked focus area – as important as “regular” maintenance – is preventive maintenance on mechanical equipment and other components. A preventive maintenance agreement with a reputable contractor can help you anticipate, plan for, and carry out maintenance projects that can significantly boost cooling tower health and longevity.
To properly diagnose maintenance issues, begin by familiarizing yourself with major cooling tower components, review manufacturers’ service requirements for these components, and use a formal checklist to guide inspections.
A generic checklist will include many items including, but not limited to:
- Tightening and changing belts
- Aligning pulleys, gearboxes, and driveshafts
- Lubricating motor bearings
- Checking for leaks
- Testing all operational and safety controls
- Cleaning cold and hot water basins as needed
- Checking and cleaning water distribution system/nozzles as needed
- Cleaning heat transfer media (fill) as needed
- Checking hardware tightness
- Checking for corrosion in basins and structure
You may also consider performing a vibration analysis to help identify potential mechanical failures ahead of time.